涂层钢板的 大优点是优良的耐腐蚀性、涂漆、装饰性和良好的成型性。近年来,汽车用涂层钢板的消耗量不断增加,已成为汽车薄板的主体。世界各国都在研究如何扩大涂层板材的品种和规格,青岛北区镀锌板,改进涂层工艺,进而提高涂层质量,即耐腐蚀性、抗粉末剥落性、涂层耐焊接性。涂层板材的成形性直是其应用的个重要方面,青岛北区2mm镀锌板,它主要取决于基体性能、涂层工艺、性能和成形工艺条件。只有综合运用先进技术,才能取得良好的应用效果。冷轧钢板由于有定程度的加工硬化,韧性低,但能达到较好的屈强比,用来冷弯等零件,同时由于屈服点较靠近抗拉强度,所以使用过程中对危险没有预见性,在载荷超过许用载荷时容易发生事故。青岛北区毛刺(或毛糙)氯化物镀锌此工艺在电镀行业应用比较广泛,所占比例高达%。乌兰察布热镀锌带钢在我国市场直是紧缺品种。从世纪年代中期以来,每年都要从国外进口-万t左右。随着国内经济的发展,尤其是汽车、家电及建筑业的发展,对镀锌带钢的需求量也大大增加。我国近来已建成了批年产量万t以上 线,但从工艺流程、设备组成到产品品种上都属于低水平传统技术的热镀锌机组,在品种质量数量上也不能满足我国经济建设发展的需求,仍需建设新热镀锌线来满足市场需要。、冷轧板硬度高,加工相对困难些,但是不易变形,强度较高。电镀锌板脱皮(或脱落)
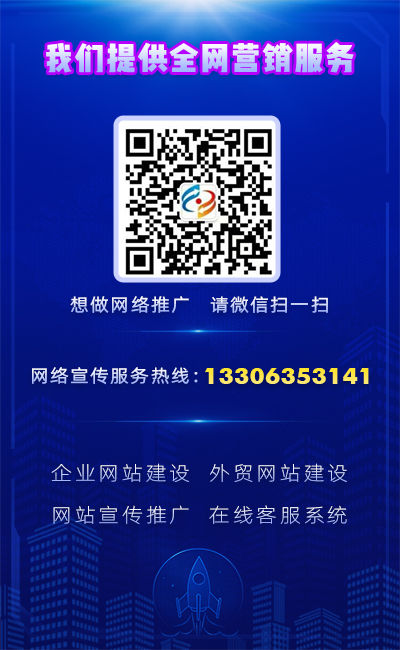
世纪年代以来,我国镀锌钢板的 取得了长足的进步,,我国镀锌钢板的加工能力已达到近万吨。国内镀锌板的市场份额迅速增长,从年的%左右增长到年的%左右。国内主要制造商为宝钢、武钢、攀钢、邯钢和本钢,总 能力超过万吨。安装、设备安装基础、空间是否合适。×××系列合金铝板×××系列合金铝板:代表。主要含有锌元素。也属于航空系列,是铝镁锌铜合金,可热处理合金,属于超硬铝合金,有良好的耐磨性。铝板是经消除应力的,加工后不会变形、翘曲。所有超大超厚的铝板全部经超声波探测,可以保证无砂眼、杂质。铝板的热导性高,可以缩短成型时间,提高工作效率。主要特点是硬度大是高硬度、高强度的铝合金,常用于制造飞机。镀锌钢板是为防止钢板表面遭受腐蚀,延长其使用寿命,在钢板表面涂以层金属锌,下游需求释放,青岛北区2mm镀锌板参考价试探性推涨,这种涂锌的薄钢板称为镀锌板,如果镀层本身质量靠谱镀锌板的防锈能力会更好些,当前青岛北区2mm镀锌板制品未来主要应用领域,镀锌板常用于各种冲压,拉伸等加工工艺中。客户至上热轧工序中,除鳞不完全,,长期提镀锌板,镀锌预埋件,预埋件产品齐全,质量过硬,价位优惠.钢板外表的氧化铁皮和夹渣残留,随后的酸洗也不能清洁钢板前皮的氧化铁皮和夹渣,但在后续的大压下量冷轧和电镀前的酸洗中,氧化铁皮或夹渣却也许在钢板的外表,致使电镀锌过程的丝状斑迹的构成。×××系列合金铝板×××系列合金铝板:代表为A。属于含硅量较高的系列。通常硅含量在-%之间。属建筑用材料,机械零件,锻造用材,焊接材料;低熔点,耐蚀性好产品描述:具有耐热、耐磨的特性。中国制造商 的热镀锌钢板主要用于建材、轻工、农业、交通等行业。由于现有的热浸镀锌设备条件、工艺技术和原板性能,可用于汽车制造的镀锌板很少。
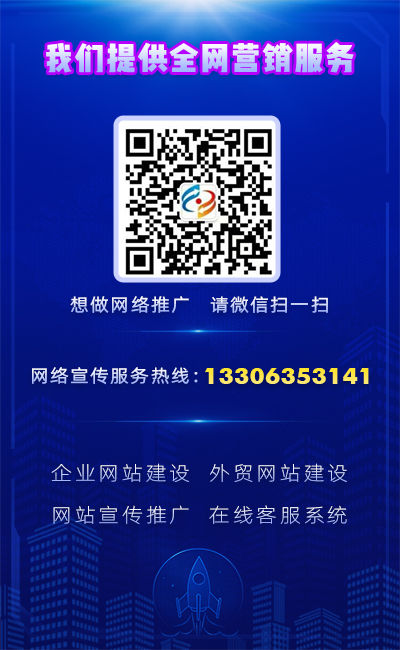
因为镉污染后的危害很大,价格昂贵,所以通常采用镀锌层或合金镀层来取代镀镉层。国内 中应用较多的镀镉溶液类型有:氨羧络合物镀镉、酸性盐镀镉和镀镉。此外还有焦磷酸盐镀镉、碱性胺镀镉和HEDP镀镉等。大家看牌号:QA-QQAF-QAQA(B)-QA(B);SPCSPCSPC性能:主要采用低碳钢牌号,要求具有良好的冷弯和焊接性能,以及定的冲压性能。如果加工程度较高,可能锌层,在使用之前请确认。因自动机的镀液少则有几千升,U形自动机镀液可多至几万升,这样多镀液调整,化工材料加少了,不作用或作用不明显;化工材加多了、加足量了,如果产生质量的原因判断错了,青岛北区高铁预埋件,加料加错了,则镀液的报废或把镀液调整回正常状态的经济损失就大了,困更多。青岛北区第方面是在汽车厂,钢卷储存时间过长,表面防锈油难于去除,所以汽车厂要好储存时间,旦出现问题,要对脱脂液浓度进行调整,极端的就是用沙皮把表面磷化层打磨掉。我国厂家 的热镀锌钢板均以建材、轻工、农业、交通等行业为主要用户。由于受现有热镀锌设备条件、工艺技术及原板性能的,实际 可供汽车制造业使用的镀锌板很少。×××系列合金铝板×××系列合金铝板:代表。主要含有锌元素。也属于航空系列,是铝镁锌铜合金,可热处理合金,属于超硬铝合金,有良好的耐磨性。铝板是经消除应力的,青岛北区2mm镀锌板的几种分类和使用,加工后不会变形、翘曲。所有超大超厚的铝板全部经超声波探测,可以保证无砂眼、杂质。铝板的热导性高,可以缩短成型时间,提高工作效率。主要特点是硬度大是高硬度、高强度的铝合金,常用于制造飞机。镀锌钢板是为防止钢板表面遭受腐蚀,延长其使用寿命,在钢板表面涂以层金属锌,这种涂锌的薄钢板称为镀锌板,如果镀层本身质量靠谱镀锌板的防锈能力会更好些,镀锌板常用于各种冲压,拉伸等加工工艺中。